Der Spezialist für Ultraschallschweißen hat ein Verfahren für eine sichere Verbindung eines ästhetischen Elements aus weichem PP in einem Haushaltgerät mit komplexer Geometrie entwickelt. Mit klassischen Methoden wäre die Wiederholbarkeit einer solchen Schweißung nicht möglich gewesen.
Die Technologie des Ultraschallschweißens hat sich permanent weiterentwickelt, sodass Ergebnisse möglich sind, die bis vor wenigen Jahren noch unerreicht waren. Schnell, sauber und effizient, dank einer Genauigkeit auf die Millisekunde. Die neuen Möglichkeiten des Schweißens wurden nicht nur durch moderne Multicore-Mikroprozessoren erreicht, die bis zu 1.000 Steuerzyklen pro Sekunde gewährleisten, sondern auch dank des immer häufigeren Einsatzes von Servomotoren. Die daraus resultierende große Anwendungsflexibilität gewährleistet, dass ein Schweißprozess in 13 vollständig einstellbare Phasen unterteilt werden kann.

Für dieses Haushaltsgerät war eine anspruchsvolle Ultraschallschweiß-Aufgabe zu lösen. (Foto: MS Ultraschall)
Die elektronische Servo-Steuerung gewährleistet eine Wiederholbarkeit der Ergebnisse, die mit klassischen Pneumatik-Steuerungen aufgrund des zufälligen Charakters der Verdichtung und der Zirkulation der Druckluft unerreichbar sind.
Anwendungen, vor allem in der Medizin, im Automobilsektor aber auch aus dem Consumer-Bereich, profitieren davon besonders. Das Ultraschallschweißen hat sich zu einem wichtigen Montageverfahren entwickelt und aufgrund seiner Vorteile aus Präzision und Wirtschaftlichkeit, vergleichbare Technologien wie dem Fügen mit Vibration, Heizplatten und auch Laser häufig verdrängt.
Herausforderung PP
Technische Polymere mit hohen Schmelztemperaturen wie PA, PPS und sogar PEEK können sicher und mit hoher Präzision verarbeitet werden. Für jede einzelne Schweißung können mehr als 200 Parameter überprüft, archiviert und analysiert werden. Unter all den komplexen Polymeren, die mit Ultraschall verbunden werden können, stellt PP ein der interessantesten Materialien dar, denn auf dem Markt gibt es mehr als 5.000 Typen und oft ist das Verhalten selbst bei sehr ähnlichen Polymeren völlig unterschiedlich. Tatsache ist, dass PP aufgrund seiner mechanischen und chemischen Beständigkeit und natürlich dank seiner geringeren Kosten im Vergleich zu anderen Polymeren, oft die erste Wahl für die technische Industrie ist.
Anforderung an den Schweißprozess
In Zusammenarbeit mit dem slowenischen Unternehmen Polycom und Bosch Hausgeräte wurde bei MS Ultraschall Technologie, Spaichingen, eine Ultraschallschweißlösung untersucht, die eine sichere Verbindung eines ästhetischen Elements aus PP, das Bestandteil eines Haushaltgeräts ist, gewährleisten sollte. Bei dem Bauteil musste eine hermetische Abdichtung und mechanische Funktionalität gewährleistet werden, da sich im Inneren Präzisionszahnräder befanden. Mit klassischen Methoden wäre die Wiederholbarkeit einer so komplexen Schweißung nicht möglich gewesen. Deshalb hat MS Ultraschall ein Verfahren entwickeln, das sowohl die hohe Dämpfung des PP als auch die für die Innenverzahnung erforderliche Präzision berücksichtigt.
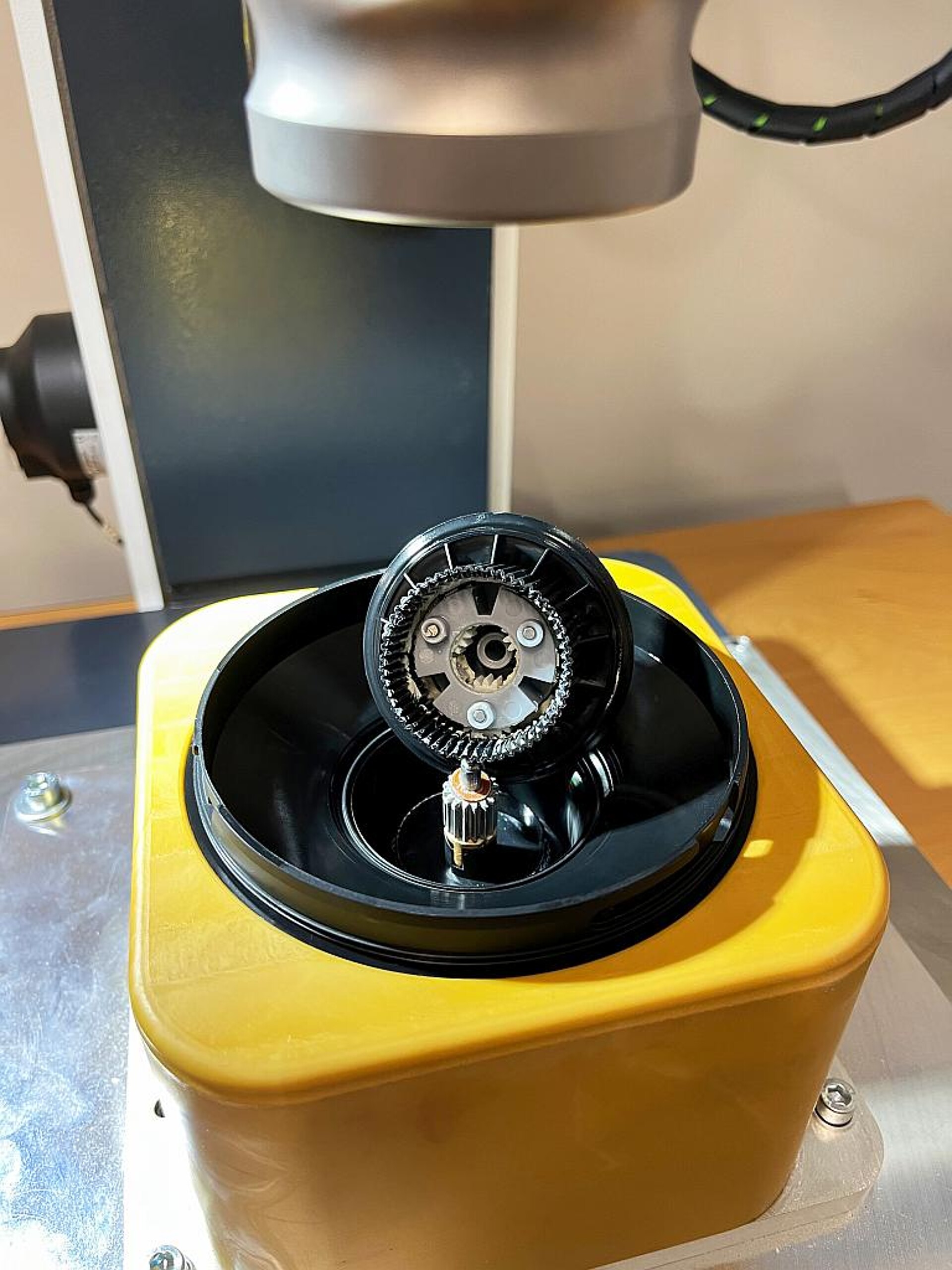
Die Herausforderung bestand in der komplexen Geometrie einerseits und der hohen Dämpfung des PP andererseits. (Foto: MS Ultraschall)
Technische Realisierung
Die erste Trigger-Phase beim Schweißprozess musste äußerst präzise sein, um sicherzustellen, dass die Schweißung immer am gleichen Kontaktpunkt beginnt. Die verwendete präzise Kraftmessdose und der Servomotor waren dabei von grundlegender Bedeutung. Die Schweißung durfte erst bei einer Druckkraft von 250 N beginnen.

Parametrisierung der zwei Phasen in der intuitiven Bedienoberfläche der Serienmaschine MS sonxTOP. (Abb.: MS Ultraschall)
Die Schmelzphase wurde in zwei Phasen aufgeteilt. Zunächst eine Aufheizphase bei angehaltener Sonotrode, dann ein Vorschub mit einer kontrollierten Schmelzgeschwindigkeit von 1,2 mm/s. Um die Toleranzen der Teile auszugleichen, reichte die Kraft allein nicht aus. Die Schmelzgeschwindigkeit sorgte dafür, dass die Kraft von Zeit zu Zeit an die tatsächlichen Fügebedingungen angepasst wurde. Um eine maximale Schweißpräzision von ± 0,03 mm zu gewährleisten, wurde auch die Haltephase in zwei Phasen unterteilt. Ein anfängliches, in Geschwindigkeit und Position kontrolliertes Halten und eine abschließende Kompression, um die Struktur des PP zu stärken und endgültig zu fixieren.
Letztlich konnte das Projekt mit Hilfe des technologischen Know-hows und den Vorteilen der Ultraschall-Schweißmaschinen MS sonxTOP erfolgreich realisiert werden.