Auf der Fakuma ist ein lokal faserverstärkter Hinterachslenker für ein Hyundai-PKW-Modell zu sehen, der im Vergleich zum Originalteil 37 % leichter ist und eine hohe Steifigkeit und Belastbarkeit bietet. Herstellbar ist dieser mithilfe der 3D-Skelett-Wickeltechnik, die in Kooperation mit der Fritz Automation jetzt im Rahmen eines Projektes auf industriellen Maßstab gebracht wurde.
Im Accord-Transferprojekt zur Industrialisierung der 3D-Skelett-Wickeltechnik (3DSW) wurde das am Fraunhofer ICT in Pfinztal entwickelte robotergestützte 3D-Faserwickelverfahren gemeinsam mit der Fritz Automation auf industriellen Maßstab gebracht. Jetzt ist die vollautomatische Serienfertigung kontinuierlich faserverstärkter Skelettstrukturen möglich. In der neuen Fertigungszelle werden thermoplastisch imprägnierte Verstärkungsfasern, wie Glas-, Natur- oder Kohlenstofffasern mit einem 6-Achs-Industrieroboter präzise auf Wickelwerkzeuge gewickelt. Die so hergestellten Faserskelette verstärken verschiedene Bauteiltypen, wie Spritzgieß-Formteile und additiv gefertigte Strukturen und können auch als leichte Skelettbauteile verwendet werden.

Der Hinterachslenker für ein Hyundai-PKW-Modell ist für die Großserienfertigung im Spritzgießverfahren konzipiert und rund 37 % leichter als das Original aus Stahlblech. (Foto: ICT)
Ebenfalls auf der Messe informiert das ICT über das Verfahren Lite2Duro und präsentiert hierzu eine Motor-Getriebe-Einheit in einem speziellen Gehäuse. Das Gehäuse wurde im Duromer-Spritzgießverfahren mit einer neuen Plastifiziereinheit von KraussMaffei hergestellt, die im Rahmen des Projektes entwickelt wurde und besonders große Schussvolumina ermöglicht. Das gezeigte Gehäuse umfasst etwa die Hälfte des maximalen Schussvolumens und konnte daher in dem 2-Kavitätenwerkzeug produziert werden. Durch Einsatz von Recyclingware sei das Bauteil zudem ressourcenschonend und umweltfreundlich. Ziel des ICT ist zukünftig die großserienfähige Prozessentwicklung.

Auf der Fakuma wird auch die Motorgetriebeeinheit mit leichtem Duroplast-Spritzgießgehäuse gezeigt. (Foto: ICT)
Leichtbau mit nur einem Material
Das Exponat einer Monomaterial-Sandwich-Sitzlehne demonstriert, wie durch spezielle Prozesstechniken und die Kombination mit thermoplastischem Schaum die Leichtbaupotenziale weiter gesteigert werden können. Die Sitzlehne, die im Rahmen eines öffentlich geförderten Projekts entwickelt wurde, besteht vollständig aus kreislauffähigen Monomaterialien.

Die Sitzlehne besteht aus verschiedenen Varianten eines kreislauffähigen Monomaterials zur Gewichtsreduktion. (Foto: ICT)
Verschiedene Materialmorphologien eines einzigen thermoplastischen Grundwerkstoffs, wahlweise PA, recyceltes PET oder biobasiertes PLA, werden kombiniert. Diese Materialien treten in Form von Fasern, Schaum und Kompaktmaterial auf, was sowohl das Leichtbaupotenzial als auch die Kreislauffähigkeit erhöht. Nach eigener Aussage konzentriert sich das ICT auf die Entwicklung der Prozesstechnik zur Verarbeitung dieser kreislauffähigen Monomaterialien auf industriell verfügbaren Anlagen.
Schlagwörter
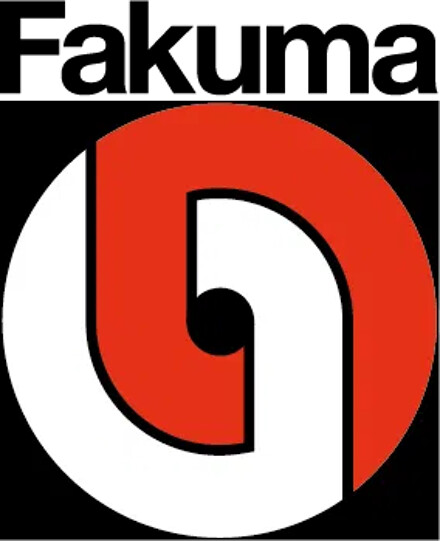