Wie sich Recyclingmaterial ästhetisch ansprechend integrieren lässt, zeigen die Engineeringspezialisten u. a. mit einem eigenen neuen Spritzschäumverfahren, das als OpenSource ohne Schutzrechte frei nutzbar ist.
Auf der Fakuma 2024 stellt Deckerform, Aichach, der Vertriebs- und Servicepartner des japanischen Spritzgießmaschinenherstellers Toyo, zwei neue Spritzschäumverfahren vor. Das marktneue Spritzschäumverfahren Deckerform PolyFoamX setzt auf Dünnwandtechnologie in Kombination mit geschäumtem Rezyklat. Deckerform bietet die Technologie als OpenSource an. Sie ist daher ohne Schutzrechte frei nutzbar.

Das neue Spritzschäumverfahren PolyFoamX von Deckerform ist als OpenSource ohne Schutzrechte frei nutzbar. Es kombiniert Dünnwandtechnik mit geschäumtem Rezyklat. (Foto: Deckerform)
„Unser Ziel ist es, dass mit diesem Verfahren möglichst viele gute und umweltbewusste Kunststoffprodukte auf den Markt gebracht werden können. In der Vergangenheit haben wir oft beobachtet, wie tolle Lösungen nicht im Alltag verwendet werden aufgrund von Schutzrechten und damit verbundenen Kosten. Das ist hier anders, wir laden ein: Nutzt unser Spritzgussverfahren Deckerform PolyFoamX! Kunststoff ist für uns genauso wertvoll wie Gold. Lasst uns gemeinsam daran arbeiten, dass Kunststoff auch in unserer Gesellschaft als Wertstoff wahrgenommen wird“, so Anna Tschacha, Geschäftsführerin bei Deckerform.

Selbst Bestandswerkzeuge, wie hier für ein Serviertablett, lassen sich ohne große Anpassungen für das neue Spritzschäumverfahren PolyFoamX von Deckerform nutzen. Im Tauchkantenwerkzeug wird zunächst eine dünne Schicht erzeugt, im zweiten Schritt per Spritzschäumen vervollständigt. (Foto: Deckerform)
Das Deckerform PolyFoamX Verfahren funktioniert wie folgt: Ein sehr dünnwandiges Vollmaterial-Spritzgießteil wird chemisch oder physikalisch hinterschäumt. „Der Clou unserer Lösung ist, dass wir das alles in einem einzigen Werkzeug machen können“, betont Plastic Engineer Peter Ottillinger. „In einem Tauchkantenwerkzeug spritzen wir zunächst das dünne Kunststoffteil. In einem zweiten Arbeitsgang können wir dieses Teil dann per Spritzschäumen vervollständigen – im gleichen Werkzeug, bei dem lediglich die Distanzstücke angepasst werden müssen. Dieses Verfahren, bei dem wir die Pionierarbeit leisten und das wir für alle zugänglich in den Markt einführen, ist eine sinnvolle Ergänzung zum In-Mold-Labeling.“
Macht auch kleine Stückzahlen wirtschaftlich sinnvoll
Das dünnwandige Kunststoffteil lässt sich zum Hinterschäumen je nach gewünschter Stückzahl manuell oder per automatisiertem Handling erneut ins Werkzeug einlegen. „Das interessante an diesem Verfahren ist, dass der Anwender nicht noch einmal in ein zweites Werkzeug oder in umfangreiche Peripherie investieren muss“, ergänzt Ottillinger. „Und das ist nicht nur unter dem Aspekt der Kosten- und Ressourceneinsparung ein interessanter Lösungsansatz.“
Klassische Recyclingmaterialien haben aufgrund vorheriger Produktlebenszyklen sowie zusätzlicher thermischer und mechanischer Belastungen im Recyclingprozess oft geringere Steifigkeitswerte. Der aktive Spritzschäumprozess ermöglicht es jedoch, durch die Expansion der Schaumstruktur die Wandstärke eines Formteils bei gleichbleibendem Gewicht zu erhöhen und somit das Widerstandsmoment zu steigern. Auf diese Weise kann die reduzierte Steifigkeit von Recyclingmaterialien weitgehend ausgeglichen werden.
Integration von Recyclingmaterialien in hochwertige Kunststoffprodukte
Mit diesem Verfahren werden zwei wesentliche Marktanforderungen erfüllt: Einerseits wird nach Wegen gesucht, Recyclingmaterialien, die bekannte Herausforderungen mit sich bringen, in hochwertige Kunststoffprodukte zu integrieren. Andererseits muss sichergestellt werden, dass die Qualität der Artikel, insbesondere hinsichtlich der Oberflächenbeschaffenheit, nicht beeinträchtigt wird. Derzeit ist es nahezu unmöglich, beide Anforderungen vollständig mit 100 % Recyclingmaterial zu erfüllen.

Ein Serviertablett dient als Muster für die neue Technologie und verdeutlicht den Einsatz von Deckerform PolyFoamX mit der Fähigkeit, selbst mit Recyclingwerkstoffen ästhetisch anspruchsvolle und funktionale Oberflächen zu erzielen. (Foto: Deckerform)
Das Deckerform PolyFoamX Verfahren ermöglicht es, auf die Oberflächen- und Nachhaltigkeitsanforderungen individuell einzugehen und beide Marktanforderungen zu vereinen. Obwohl es sich um ein 2K-System handelt, kann es durch die Verwendung eines Kombiwerkzeugs und bestehender Fertigungsanlagen hergestellt werden, sodass die vorhandenen Ressourcen optimal genutzt werden.
Hinterschäumen von Organosheets
Neben dem marktneuen Spritzgussverfahren Deckerform PolyFoamX stellt Deckerform das Hinterschäumen von Organosheets als weitere Branchenneuheit vor. Die Exponate am Deckerform-Stand stellen das Hinterpressen und Hinterschäumen von Organosheets in den Fokus. Auch hier gilt es, die spezifischen Vorteile der unterschiedlichen Materialien intelligent zu nutzen. Organosheets sind thermoplastische Polymerfolien, die mit Geweben oder Gelegen aus Kohle-, Glas- oder Aramidfasern verstärkt sind. Oft entstammen die Gelege oder Gewebe zudem dem Recycling von Carbonwerkstoffen.
Die hohe Zugstabilität der Organosheets und der materialsparende, effiziente und sehr steife Leichtbau aus dem Schäumen ermöglichen besondere Bauteileigenschaften. Damit sind solche Kombinationen interessant für ein breites Spektrum an Teilen etwa im Automobilbau, im Sport- und Freizeitbereich, aber auch in der Medizintechnik oder in Architektur und Bauwesen. „Wir bei Deckerform wollten uns diese Eigenschaften zu Nutze machen und haben seit dem letzten Jahr intensiv an der Kombination aus Spritzschäumen und der Einbindung der Organosheets geforscht. Jetzt können wir erstmalig auf der Fakuma unsere Erfolge dazu vorstellen“, so Anna Tschacha.
Pionierarbeit im Stuhldesign
„Wir haben in unserer Ideenschmiede für einen zukunftsweisenden Stuhl das komplette Engineering übernommen und die Spritzgusswerkzeuge gebaut“, erklärt Tschacha. „Dazu gehören die Beinschalen, die bei diesem Konzept die Sitzfläche ersetzen, und deren produktionstechnische Auslegung. Sie entstehen in einem Monosandwich-Verfahren, bei dem zunächst die äußere Schicht aus PP gespritzt wird und dann in einem zweiten Schritt der entstandene Hohlraum mit einem glasfaserverstärkten PP-Werkstoff gefüllt wird. Das ermöglicht stabile und dabei doch sehr flexible Beinschalen, die sich an den Körper des Nutzers und dessen Bewegungen optimal anpassen.“ Ebenfalls von Deckerform konzipiert und umgesetzt ist das Werkzeug für die dazugehörige Feder aus glasfaserverstärktem PP, die dem Stuhl die nötige Elastizität gegenüber seinem Gestell verleiht.
Live-Produktionen auf vollelektrischen Spritzgießmaschinen
Live produziert Deckerform am Messestand einen Getränkeuntersetzer im Broken-Ice-Design aus dem Recyclingwerkstoff rPET. Die Anwendung läuft in einem Wechselwerkzeug von Deckerform auf einer vollelektrischen 500-kN-Spritzgießmaschine von Toyo. Vollelektrische Spritzgießmaschinen sind aufgrund ihrer Energieeffizienz ein wichtiger Bestandteil in nachhaltigen Produktionskonzepten.
Die eingesetzte vollelektrische Spritzgießmaschine Si-50-6s D75E verfügt über eine Schnecke mit Durchmesser 28 mm und ermöglicht ein theoretisches Einspritzvolumen bis zu 69 cm³. Die kompakte Maschine mit rund 2,8 t Gewicht bietet einen Holmabstand von 360 x 360 mm. „Damit kommt man in dieser Werkzeugklasse in der Regel sehr gut zurecht“, erklärt der Anwendungstechniker Maximilian Allesch. „Auf der Maschine sind Werkzeuge bis zu einer Plattengröße von 500 x 500 mm möglich.“
Der Getränkeuntersetzer ist KI-unterstützt designt und kommt als frei fallendes Teil aus dem Werkzeug. Deckerform nutzt zur Oberflächenveredelung die Oberflächenstruktur des Werkzeugs. Darüber hinaus können Besucher ihren Getränkeuntersetzer direkt am Messestand an zwei Durchlauf-Heißprägemaschinen selbst weiter aufwerten und als Give-away mit nach Hause nehmen.
Energieeffiziente Verpackungsproduktion

Auf der vollelektrischen 2.800-kN-Spritzgießmaschine Si-280-6s JH600E in Packaging-Ausführung von Toyo läuft eine energieeffiziente Verpackungsanwendung im 5-s-Zyklus. (Foto: Toyo)
Auf High-Speed getrimmt ist die Live-Packaging Anwendung am Toyo-Stand (A5, Stand 5208). Auf einer vollelektrischen Toyo-Spritzgießmaschine Si-280-6s JH600E mit 55 cm Schneckendurchmesser entstehen Teile, die für die Verpackungsindustrie typisch sind mit einem minimalem Energieverbrauch 0,23 kWh pro kg verarbeitetem Polypropylen. „Die Maschine ist in Packaging-Ausführung konfiguriert“, erläutert Tschacha. „Das bedeutet, dass die Maschine mit schnelleren Antrieben ausgestattet ist und der Spritzzylinder auf ein Längen-Durchmesserverhältnis von 24 erweitert ist. Die Maschine ist auf schnellere Öffnungs- und Schließzyklen ausgelegt als die Standardausführung.“ Ein Highlight ist der angesichts der Leistungsfähigkeit und Größe der Maschine geringe elektrische Anschlusswert von 87 kVA. In der Anwendung auf der Fakuma arbeitet die Maschine in einem 5-s-Takt.
Schlagwörter
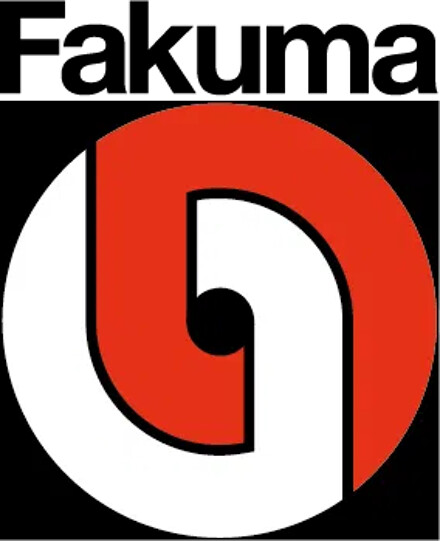